How the lumber industry misread Covid and ended up with a global shortage and sky-high prices
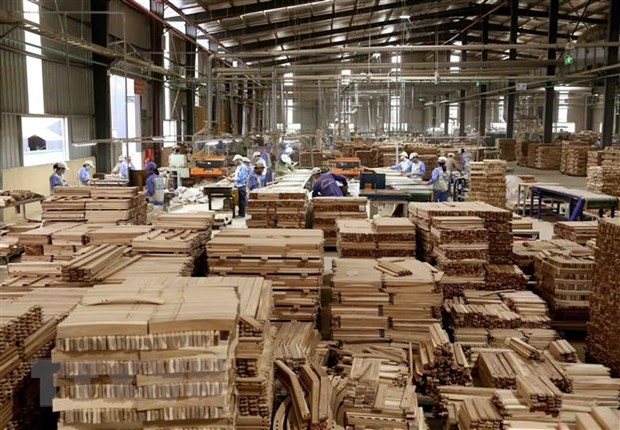
A pandemic surge in home buying and renovation sent lumber prices soaring. They may never return to normal, experts say.
As home building and renovation soared amid pandemic lockdowns, the price of lumber rocketed from around $400 per thousand board feet in February 2020 to an all-time high of over $1,600 in early May. Prices have since fallen to the $800 range — still nearly double their pre-pandemic rates — in what could potentially be the new level for the near term.
In April, as lumber prices hovered around $1,200, the National Association of Homebuilders estimated that the rise in lumber prices had added over $36,000 to the cost of a new single-family home.
The lumber and home construction industries' misread of the economic impact, as well as Covid-related restrictions on production, and a ten-year period of under-building of new homes since the 2008 financial crisis, set the stage for undersupply as demand surged, experts say.
Seeing the temporary economic decline due to the lockdowns and coronavirus outbreak, lumber producers, like so many other manufactures, took a page out of their recession playbook, cut back production and took downtime, said Eric Kingsley, a forest economist and partner at Innovative Natural Resource Solutions, a consultancy with offices in New Hampshire and Maine.
“The assumption was...that housing starts, which is where most lumber goes, would decline,” he said of new homebuilding, and that there would be a lull. “That turned out to be false.”
A spokesperson for the lumber industry said it had in fact been predicting "pretty good housing starts" and the shutdowns were "all about employee safety," said Susan Yurkovich, president and CEO of the Council of Forest Industries, an industry lobbying group for Canadian producers, a large supplier of softwood structural lumber for the U.S.
The price jump was "a classic case of supply and demand imbalance," that followed a "massive supply chain disruption" due to Covid. "Never before in history have we had that kind of price appreciation so quickly," Yurkovich said.
Mills temporarily shut down to implement new safety protocols and acquire personal protective equipment. Some mills took down time. Others had to cut back production because workers got Covid. Mills were short-handed when demand hit.
Home buying roared as consumers who still had jobs — and income to spare — exited cities for suburbs, springing for a second home or a new remote working situation with space for their family to spread out.
Workers who stayed in their existing homes added home office additions or took care of long-delayed home renovation and expansion projects. Historically low interest rates and a flow of easy money policies made it easier than ever for buyers to cash in the 401(k) accounts and snap up second and third homes.
All this stressed lower supplies and labor, pushing prices upward and creating the opportunity for more extreme spikes in prices.
Also at play were large buyers, who bought up lumber ahead of further rising prices, further constraining supplies.
Workers build residential single family homes in Valley Center, Calif., on June 3, 2021.Mike Blake / Reuters
“More people were locking themselves into contracts to make sure they have adequate supply. That took more wood off the open market,” said Brian Leonard, a lumber analyst with RCM Alternatives. “You had a lot of buyers chasing less wood.”